
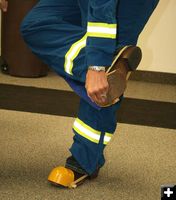
Clackers
"Clackers" are metal toe caps worn over shoes to protect feet while working on a drill rig site. All tour visitors had to put these on over their street shoes. They are called clackers because of the noise they make walking on the metal drill rig stairs and corridors.
|

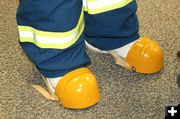
Clackers
|

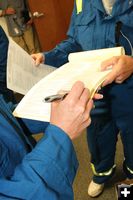
Safety Release
Everyone had to listen to the safety briefing, then sign the Safety sheet saying they have read, understand, and agree to abide by the requirements and responsibilities listed in the Jonah site specific safety and environmental briefing. The 25-point briefing covered accidents, injuries, fall protection, clothing, smoking, wildlife, horeseplay, tools, photographic devices, housekeeping, driving, firearms, explosives, weaponds, working in extreme temperatures and other operations. "You have the authority and responsibility to stop any unsafe operation."
|


Shuttle Bus
Workers, and tour visitors, are moved around in these shuttle busses. They hold 25 people each and help to significantly reduce the amount of vehicle traffic moving around the gas field. Shuttle services are provided by Sublink Stage.
|

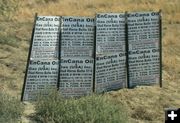
Well signs
Rig signs
All the wells are signed with their name, number, location, lease number and emergency contact information.
|

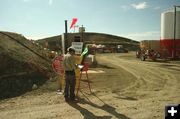
Signing into the drill site
Everyone who goes on a drill site must sign in and out.
|

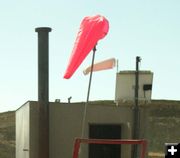
Wind sock
All the sites have wind socks to let workers know the direction of the wind in case of an emergency.
|

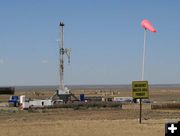
Muster areas
Each drill pad has two emergency muster areas on opposite sides of the pad, for gathering areas for workers to stay upwind in case of an emergency.
|

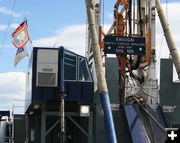
Ensign Rig 129
Encana contracts with third party suppliers to provide the drill rigs and do the drilling and completion work. Encana does not own any of the drill rigs. This rig is run by Ensign. Operations are controlled from the "dog house", a small room on the rig floor used for the drilling control operations.
|

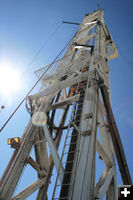
Drill Rig
Much of the work on the rig floor has been automated, making it much safer for rig workers. However, someone still has to climb the rig tower daily, summer and winter while it is in operation, to do maintance. This requires special safety rigging to protect from falls.
|

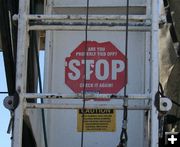
Are you tied off?
Warning signs warn workers when there are hazardous conditions nearby. Workers must be connected to safety ropes before climbing the drill rig.
|

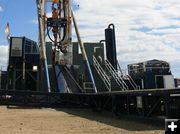
Drilling pipe
During the drilling process, the pipe segments are staged on a platform near the rig, then drawn up automatically as each segment is needed as the hole is dug deeper into the ground. Ultimately, this rig will drill to a depth of around 13,000 feet to reach the natural gas layers.
|

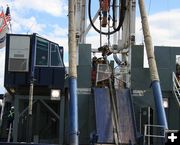
Lifting up
The elevator lifts the pipe up and moves it into position.
|

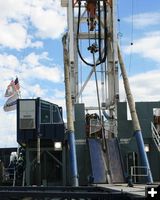
Up and over
The pipe is lifted up and fitted onto the pipe that is already in the ground.
|

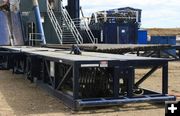
Next pipe
The "mule" lifts and moves the next piece of pipe automatically into position on the feeder of the drill rig during drilling.
|

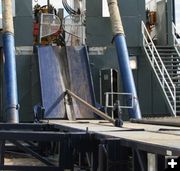
Feeding the pipe
The feeder automatically moves the next segment of pipe into position on the rig. A lot of automation has been implemented in the last ten years eliminating much of the manual labor, and danger, that used to be part of the work on the drill rig.
|

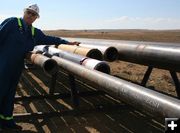
Drill pipe
Rick Felker explains the different kinds of drill pipe used to drill the gas well.
|

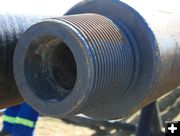
Pipe fitting
|

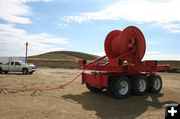
Drill line
Drill line control cable is fed in during the drilling process.
|


Drilling
This is where the pipe is being drilled into the ground.
|

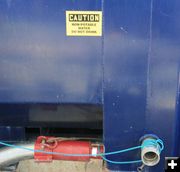
Non-potable water
|

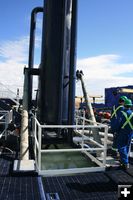
Drilling water
Water is mixed with mud to aid the drilling process. This water is cleaned and used over and over again.
|

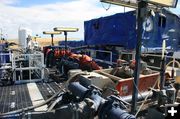
Drill rig platform
The drill rig floor is a metal platform over the top of various tanks and equipment. It takes 4 to 6 people to operate the rig in the drilling process.
|

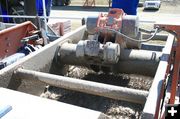
Separating the cuttings
The cuttings are the solids removed from the borehole during the well-drilling process. It is usually made up of sands, shales and the other rock encountered as the drill bit moves through the underground rock formations. The drill cuttings are removed by circulating the drilling fluid over shale shakers. The shaker typically consists of large, flat sheets of wire mesh screens or sieves of various mesh sizes that shake or vibrate the drill cuttings across and off of the screens as the drilling fluid mud flows through them and back into the drilling fluid system. This separates the solid drill cuttings from the fluid so that it can be recirculated back down the wellbore.
|

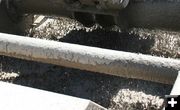
Jumping cuttings
The cuttings jump up along the vibrating shaker and are separated from the drilling fluid mud.
|

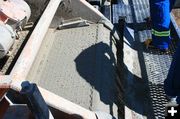
Cuttings
Million-year old dirt remains after the shaking process.
|

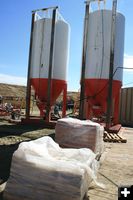
Mud
Pallets of bags of drilling mud are use in the drilling process.
|

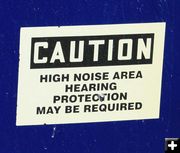
High Noise areas
Workers wear earplugs for ear protection in high noise areas.
|

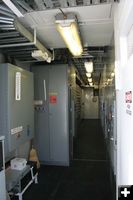
The brain
The control room is the brain of the rig operation.
|

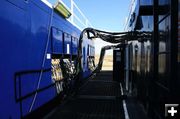
Plugged in
The brain is plugged into the drill rig.
|

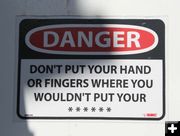
Danger sign
|

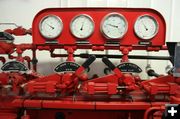
Pressure gauges
|

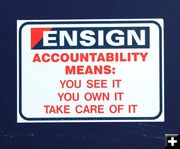
Accountability
Ensign sign: Accountability means: You see it. You own it. Take care of it.
|

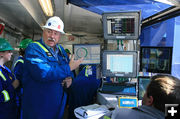
Dog House
Rick Felker explains the monitors and controls in the "dog house".
|

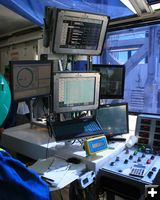
Monitors
|

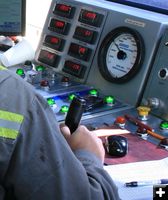
Joystick controls
The older generation drillers kid the younger generation about the computerized joystick controls in the modern drill rigs, similar to the controls on the computer games many of the new workers grew up on and are very familiar with using.
|

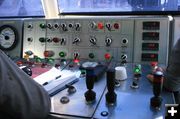
Game Boy Drill Rigs
The kids playing computer games today will feel right at home when they move into a job in the control room of a drill rig.
|

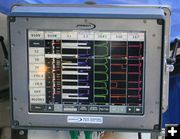
Control monitor
The drill bit is a 9,108 feet depth in the wellbore of Stud Horse Butte 121-9. It will drill down to about 13,000 feet in all, which will take 3-4 more days. The technology has advanced so much in the past 10 years it takes just 10-12 days to drill a well now. It used to take 95-120 days.
|

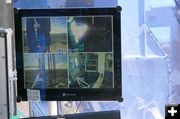
Camera monitors
|

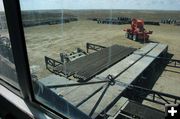
Drill pipe
View of the pipe pick up from the dog house. So much is automated now on the drill rigs, employees work in a much safer environment than the old days. The reality-TV show "Black Gold, " which chronicles three oil drilling rigs in Andrews County, Texas, has done a lot to damage public perception about the reality of the high safety standards on the new generation gas drilling rigs used in Wyoming.
|

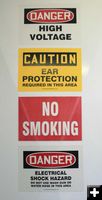
Danger, Caution, Danger
|

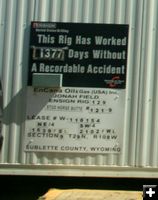
1377 days without an accident
Ensign Rig#129 has worked 1377 days without a recordable accident.
|

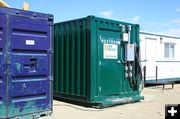
Restroom
The company manager and geologist live in trailers on the site and stay full-time. All the equipment is industrial scale and modular, so it can be packed up and moved over to the next drilling site.
|

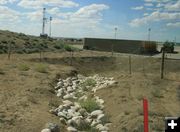
Erosion control
|

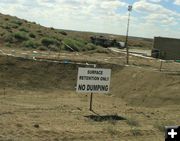
No dumping
Everything is well signed throughout the field with caution warnings and identification signs.
|

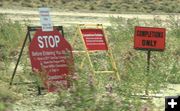
Authorized Personnel Only
|

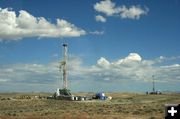
300-400 more to go
The drilling program is winding down with only 300 - 400 wells left to drill in Jonah. The existing wells should produce for another 30 to 40 years, at a declining rate. The NPL will be located adjacent to the Jonah, allowing Encana to utilize a lot of their existing infrastructure.
|

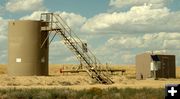
Jonah
|

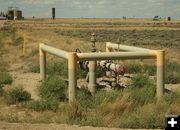
Jonah
|

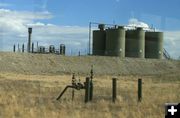
Jonah
|

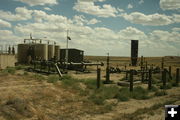
Jonah
|

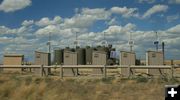
Jonah
|

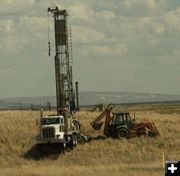
Drill truck
Drilling a water well? We're not quite sure what is going on in this photo, but the truck looked very interestingly positioned.
|

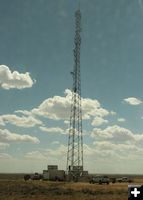
Communications tower
The blobs at the bottom and about halfway up this tower are maintenance workers.
|

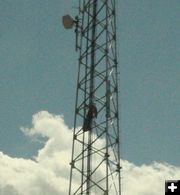
Tower climber
|

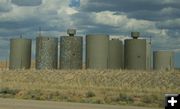
Camoflauge
A lot of work has been put in to try and find colors and patterns to make the structures on the gas fields blend in and be less visible on the landscape.
|

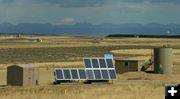
Solar powered
Right now, power is provided by solar panels, generators and other kinds of engines. Pacific Power is putting in powerlines that eventually with electrify the entire Jonah Field. That is expected to significantly cut down emissions that are causing ozone and air quality issues.
|

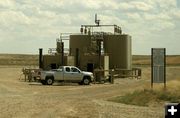
Central Delivery Facility
|


Spill containmemt
A stock watering tank serves a new purpose acting as a spill catch basin for tanks at well sites. Wire mesh is placed ver the top to keep birds and other animals from getting into the tank.
|

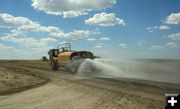
Water truck
Water trucks keep the dirt roads watered to keep down the dust.
|

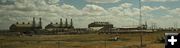
Bridger Compressor Station
Product is piped to this central gathering facility where it is pumped into pipelines to go to market.
|

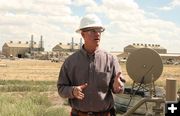
Randal Phillips
Randal Phillips, Encana EIS Project Manager, said the company is working with the Bureau of Land Management and Rocky Mountain Power to bring electric power to their facilities in the Jonah and the NPL. Electricity will eliminate the need to burn natural gas or other fuels that create emissions that may contribute to air quality concerns.
|


Workforce Facility
|


Workforce facility
|

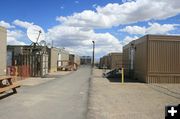
Workforce Facility
The Workforce Facility houses nearly 300 people, including Encana company people, subcontractor employees and staff. It has dorm rooms, a dining hall, rec center, offices, and outdoor recreation areas. It has its own power plant and water treatment complex. Entrance and exit is through a gated security check station. The complex has no alcohol, drugs, firearms or dogs.
|

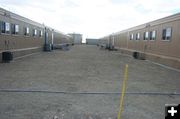
No grass
All of the buildings in the Workforce Facility are modular and will be hauled off once they are no longer needed. The outsides don't have grass or landscaping. The insides have all of the comforts of home, and more.
|

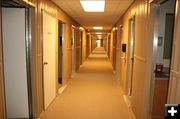
Dorm Hallway
|

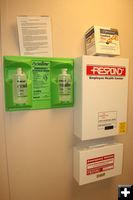
First Aid Station
First aid stations are located in the hallways of the dorm trailers.
|

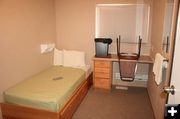
Dorm room
Workers get their own private room which includes a bed, desk, closet, and 19-inch flat screen TV. The complex has internet access.
|

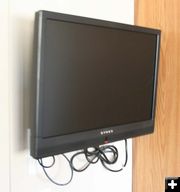
Flatscreen TV
Each dorm room has a 19" flat screen TV.
|

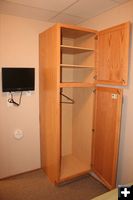
Closet
Each dorm room has a closet for putting clothes.
|

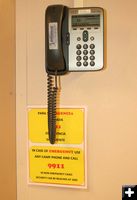
Hall phone
Phones are located in the dorm hallways.
|

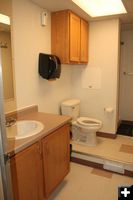
Hall bathroom
Bathrooms and showers are located in the dorm trailers.
|

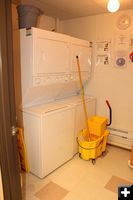
Washers and Dryers
Each dorm trailer has a laundry room with washers and dryers. These are free to use.
|

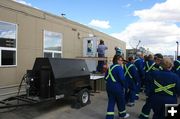
Dining Room
In addition to giving the tour of the gas field, Encana let the tour group eat at the Workforce Center dining room and try the camp food. (It was delicious.) Sometimes the menu includes BBQ meals.
|

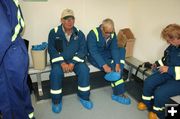
Booties
Members of the public tour put on booties over their shoes in the Workforce facility dining room, just like the workers have to, in order to keep the carpet clean.
|

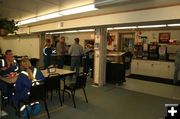
Dining Room
|

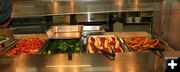
Dinner
This meal includes pasta, broccoli, sloppy joes and onion rings and ranch toast. Additional food, salads, breads and desserts were in the coolers.
|

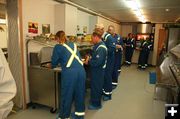
Dining Room
|

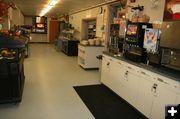
Serving area
Dining room serving area.
|

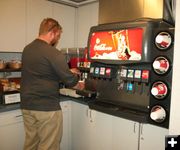
Drink center
|

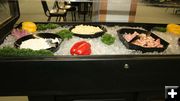
Salad Bar
|

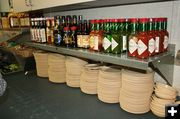
Steak and hot sauces
|

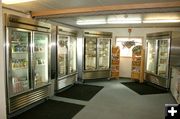
Grab n Go coolers
Workers can grab whatever they want and as much as they want from the dining room, and it's free to them.
|

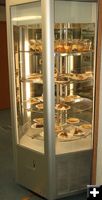
Desserts
|

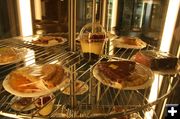
Desserts
|

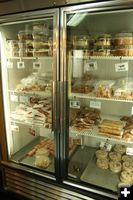
Grab n Gos
Stir fry, poppers, Chicken Cordon Bleu, chimichanga, chicken strips, chicken floutas, pizza, corn dogs, egg rolls, macaroni & cheese, taquitos, kielbasa...
|

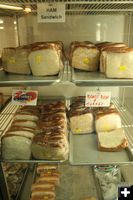
Sandwiches
Ham, roast beef, turkey sandwichs, hotdogs...
|

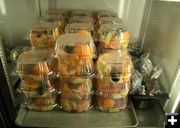
Fruit
|

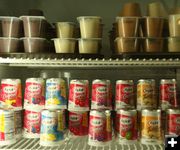
Yogurt and pudding
|

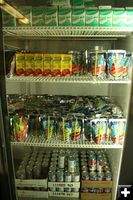
Drinks
|

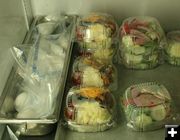
Salads and boiled eggs
|

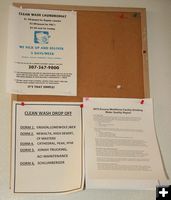
Bulletin board
Bulletin boards post information and notices. This one has information about laundry pick-up and delivery and the Workforce Facility Water Quality report.
|

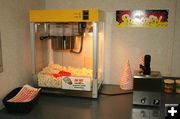
Popcorn
There's even a popcorn machine in the dining room for a snack.
|

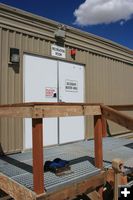
Rec Room
We didn't have time to go into the Rec Room in the Workforce Facility on this tour, so we don't have pictures to show you of the interior. But we can relay that the Rec Room has a variety of exercise equipment, ping pong tables, large screen TVs, lounge chairs and tables, and computers for internet access.
|
|